Image: Sensor Networks
As the 2020 US DOT’s Pipeline and Hazardous Materials Safety Administration (PHMSA) “Mega Rule” affects pipeline companies, Sensor Networks is partnering with clients to assess and monitor corrosion in decades-old pipelines with ultrasound sensors. This technology has been helping companies harvest data in order to understand corrosion rate and activity, and the effectiveness of their operations to combat corrosion as never before. Beyond regulatory compliance, it’s been saving miles of pipeline, eliminating downtime and boosting productivity. And recently, it also saved one company $6 million.
“Because of COVID, companies were not able to have as many technicians on site—in many cases only 10% of their normal workforce,” says Steve Strachan, vice president of sales, Sensor Networks. “So they had to find a way to do more with less. Fortunately, that’s where sensor technology is at its best: placing sensors not only in hard-to-reach areas, unmanned, or inaccessible entry points, but now using them to save costs and maintain or even increase efficiencies during a workforce crisis.”
“The client said that they’d never been able to glean this kind of corrosion information before. This data helped them to be able to better understand metal-loss activity at different locations of their assets and the effectiveness of their operations to combat corrosion.”
On July 1, 2020, Phase 1 of the widely-anticipated PHMSA ‘Mega Rule’ went into effect. Simply put, it outlines measures meant to prevent pipeline spills and deadly gas explosions in the 500,000-plus miles of pipelines that carry natural gas, oil and other hazardous materials throughout the U.S.
Market challenges have become a catalyst for much-needed automation changes
“Because of the costs and uncertainties associated with permitting, legal and changing political climates,” says Strachan, “many asset owners have been forced to change their strategy. They need to pivot from new construction and instead focus on protecting and extending the lives of their precious infrastructure that is already living under or above ground. They also need to find smarter ways of using asset integrity planning and monitoring techniques in order to maintain their normal (and expensive) inspection intervals.”
That’s where Sensor Networks, Inc. comes in. The company’s smartPIMS ultrasonic system includes wireless multi-sensor transmitters that monitor ‘active’ (or likely active) areas or anomalies along a pipeline, to be able to tell an asset owner the corrosion rate in that given area. The data the transmitters gather allows the users to track the speed at which the asset is corroding, to be able to determine when to perform a maintenance activity before there is leak, rupture or spill.
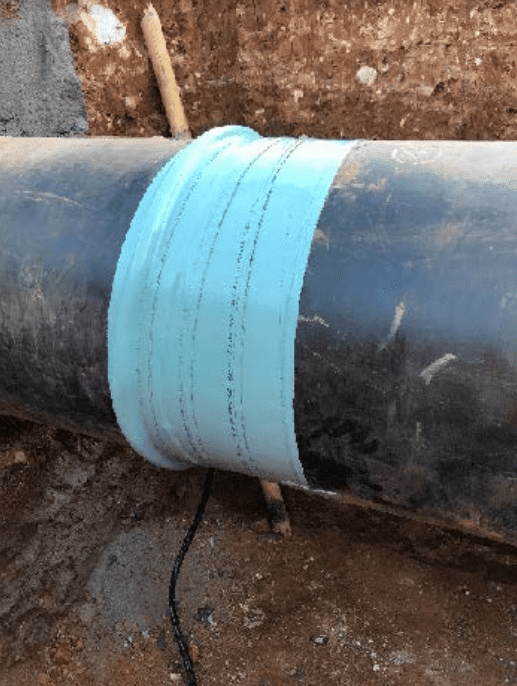
Sensors covered with protective coating
The solution not only satisfies compliance requirements, but also provides valuable asset integrity information and insight, allowing for preventive maintenance activities that haven’t been possible before using these sensors.
“The past few years in particular have posed a lot of challenges for energy companies,” Strachan says. “With COVID, new regulations and extreme downward fluctuations in the price of oil, companies have had to change their thinking to stay profitable. Those challenges have actually been a catalyst for some positive change. It’s like finally starting a solid gym regimen and that great feeling of being in shape and living a healthy lifestyle, and thinking ‘Why didn’t I do this year’s ago!?’ Companies are finally starting to use automation and they are finding that they have so much more access to timely, quality data and can make better decisions, than they ever had before.”
Push for automation saves one customer $6M
In early 2020, one Sensor Networks customer’s push for automation saved millions. They found a cluster area that lost between 0.040”- 0.089” of thickness in a few critical areas along the pipeline since the last internal inspection. They decided to install a smartPIMS ultrasonic system to monitor the pipe and glean corrosion data. Data was collected and analyzed at the end of the month. The asset owner was able to quickly and accurately trend the corrosion rate and work to remediate the issue. After they worked to fix the issue, the sensors also flagged when the corrosion inhibitor’s effectiveness declined, allowing them to switch to a new inhibitor to improve the outcome.
“Our customer is going to save an estimated $6 million with an investment of $25,000 in sensors. That’s an ROI and payback period of well north of 100% in just six months.”
“This section of pipeline was built in 1974,” says Strachan. “There were over 45 integrity digs since the pipeline was laid, which span this 500-mile section with costs estimated at around $20 million in ground removal, construction, inspection and maintenance — and that’s not even accounting for lost revenue due to downtime. Once putting the sensors in place during their last integrity dig and monitoring the corrosion for a short six-months, the client said that they’d never been able to glean this kind of corrosion information before. This data helped them to be able to better understand metal-loss activity at different locations of their assets and the effectiveness of their operations to combat corrosion.”
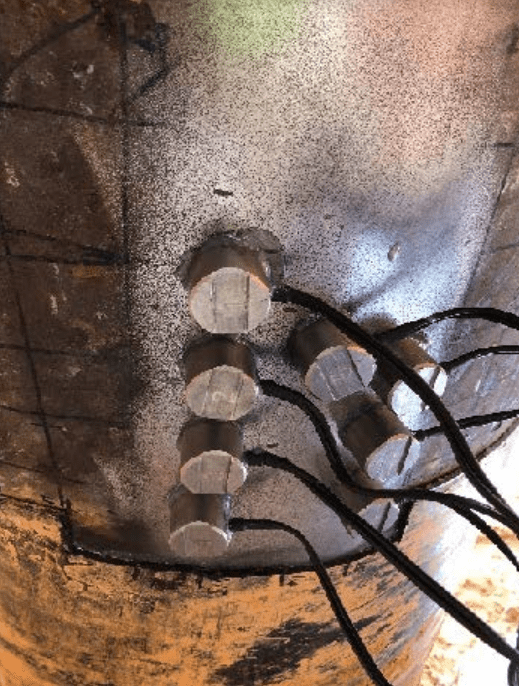
Dual-element sensors installed permanently on identified cluster of ‘low spots’ on six-o’clock position of pipeline
The data that Sensor Networks’ smartPIMS system provided allowed the operator to maintain their normal inspection intervals. They were able to save costs on cleanings and chemicals, and eliminated the need to take the asset offline while sections of the pipeline were repaired, allowing them to extend the life of the asset until maintenance is necessary. These items alone are estimated to save the operator $6 million in the next five to seven years.
“Our customer is going to save an estimated $6 million with an investment of $25,000 in sensors. That’s an ROI and payback period of well north of 100% in just six months,” says Strachan. “The ability to have access to this invaluable data and be able to monitor, and in this case, mitigate the corrosion, has allowed this asset owner to safely and confidently operate the line for years to come.”