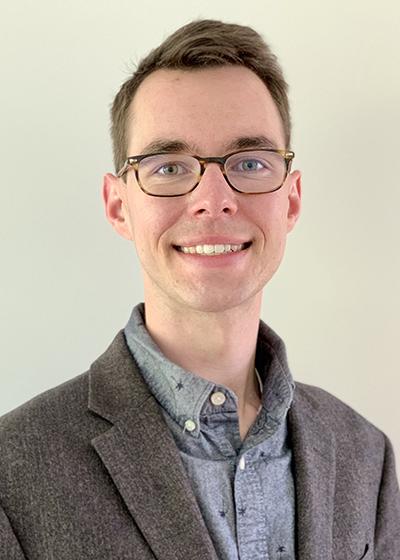
A group of Penn State researchers that received a $1.2 million grant from the U.S. Department of Energy’s Advanced Research Projects Agency-Energy is aiming to improve the efficiency of turbines for power generation through the use of artificial intelligence.
Wesley Reinhart, assistant professor of materials science and engineering at Penn State, said that higher efficiency is achieved at higher operating temperature, but few materials can maintain structural integrity above 2000°C, which is why their team is investigating a special class of metal alloy called refractory high-entropy alloys that fit the bill for this application. However, these alloys are very complicated to design and expensive to test, which is why they’re using artificial intelligence to accelerate the scientific process.
“The exciting thing about this project is that we are developing both advanced materials and a general-purpose, AI-driven design strategy at the same time. I think we are just beginning to see the benefits of AI in science and engineering, as many of these technologies were developed by the computer vision community for more niche applications like self-driving cars or AI-based video editing (i.e., deepfakes),” Reinhart says. “The advances made here could readily transfer to other challenging materials design problems such as for electronics or biomedical devices, which would greatly broaden our impact.”
“We are just beginning to see the benefits of AI in science and engineering.”
The scientists trained a generative adversarial network to create novel refractory high-entropy alloys, materials that can withstand ultra-high temperatures while maintaining their strength and that is used in technology from turbine blades to rockets. According to Reinhart, the AI will identify patterns linking design and performance characteristics that human experts can’t find due to their complexity and the large amount of data that needs to be analyzed.
“If this works, it could revolutionize the way we design new materials – making the entire process faster, cheaper, and more effective, thus reducing the detrimental impact of materials research and development to the environment,” Reinhart says.
The team combed through hundreds of published examples of alloys to create a training dataset. The network features a generator that creates new compositions and a critic that tries to discern whether they look realistic compared to the training dataset. If the generator is successful, it’s able to make alloys that the critic believes are real, and as this adversarial game continues over many iterations, the model improves. After this training, the scientists asked the model to focus on creating alloy compositions with specific properties that would be ideal for use in turbine blades.
Since the start of this project in May, the team has implemented the AI and supporting cyber-infrastructure, trained the models on data from the scientific literature, and deployed the model to design a batch of alloys to test the performance of their AI model.
“This first batch is being synthesized right now here at University Park, and we look forward to receiving the measurements to evaluate the accuracy of the predictions made by our AI scientist-in-training,” Reinhart adds. “This puts us right on schedule, and we plan to accelerate the pace of new materials being designed and tested as the model becomes more accurate with experimental feedback.
“If this works, it could revolutionize the way we design new materials – making the entire process faster, cheaper and more effective.”
Earlier this fall, the researchers published their first findings in the Journal of Materials Informatics. The preliminary results published in the journal show that generative models can learn complex relationships to generate novelty on demand, making them a valuable tool for materials informatics.
Reinhart indicates that the next steps in the project are to perform more in-depth modeling and characterization of the mechanical properties of the newly designed alloys.
“Up to this point we have mostly been building infrastructure to get the first batch of alloys created and tested – the first sample is often the most challenging since everything is being put into place for the first time,” Reinhart says. “These materials won’t see field testing unless the project is selected for Phase 2 funding by ARPA-E.”
According to the US Department of Energy, the Ultrahigh Temperature Impervious Materials Advancing Turbine Efficiency program, which funded the research being done at Penn State, consists of two separate phases, which may be proposed for a maximum of 18 and 24 months, respectively. In Phase I, project teams will demonstrate proof of concept of their alloy compositions, coatings, and manufacturing processes through modeling and laboratory-scale tensile coupon (sample) testing of basic properties. In Phase II, approved project teams will investigate selected alloy compositions and coatings to evaluate a comprehensive suite of physical, chemical, and mechanical properties as well as produce generic small-scale turbine blades to demonstrate manufacturability.