A Penn State professor has collaborated with researchers in China to develop an “electronic skin” sensor that mimics dynamic human motion, and their breakthrough could change the future for severely disabled people.
Huanyu “Larry” Cheng is Penn State’s Dorothy Quiggle Early Career Professor in engineering science and mechanics, and he’s been named on Forbes 30 Under 30 in Science for his work on biologically-inspired electronics for use in robotics. He says the sensor his team has developed could be a major step forward for the development of smart robotics.
Teaching smart robotics by mimicking human movement
“The skin of the human hand is amazing, and that’s what we tried to imitate,” Cheng said. “How do we capture texture and force? What about the years of evolution that produced the impressive sensitivity of the fingertip? We’re attempting to reproduce this biological and dynamic process to enable objects to behave similarly to the human hand.”
The sensor measures both the magnitude and load of movement, calculating data such as the effort required to swing a tennis racquet, along with rate, duration and direction.
The team had to analyze the measurements to understand how the separate parameters influenced each other. For example, bouncing a tennis ball gently on a racquet requires different input than serving a ball to an opponent. Those variables are critical for someone with a prosthetic arm who needs to differentiate between handling an egg or carrying a watermelon.
Cheng says these sensors can help capture the magnitude for pressing, bending and manipulating delicate objects. The sensors could be used for soft robotics in applications like catching fish, or even in a disaster when a robot may be needed to crawl through irregular spaces and move debris.
How it works: precision sensor allows for both force and flex
To develop their dual-mode sensor, the team looked at other models and sensors that worked, and created something brand-new. They came up with a sensor that is informed by dual signals: piezoelectric and piezoresistive. The piezoelectric signals measure outside force, like pressure, and this creates electrical charge, and the piezoresistive signals mitigates the current.
Then, taking both sensors for piezoelectric and piezoresistive signals, the team sandwiches the dual-mode sensors together, facing two internal layers of pyramid-shaped microstructures toward one another. These microstructures gather and interpret data from both layers, taking information on magnitude and duration measurements from the piezoresistive layer, and dynamic loading rate and direction from the piezoelectric layer. This synergy of data allows for precision measurements of force and flexibility, allowing for highly-specific movements.
Helping amputees regain mobility
Cheng sees the potential for this technology to help amputees regain independence and mobility. “The technology can help people who have lost their limbs from an accident, or disease, or war. These sensors can provide an interactive human-machine interface and give them back their mobility, allowing them to operate external objects with ease again.”
Penn State has filed a provisional patent for the technology, and Cheng says the team is moving on to integrate the dual-mode sensor with the other sensing modalities to result in a multimodal device with extended capabilities for biomedicine.
As they continue development, Cheng says their sensor will benefit industry far beyond medicine and prosthetics. “Because of the demonstrated capabilities of the dual-mode sensor in intelligent robots and future human-machine interfaces, I think that many smart manufacturing companies and robotics companies will benefit from this technology,” he says.
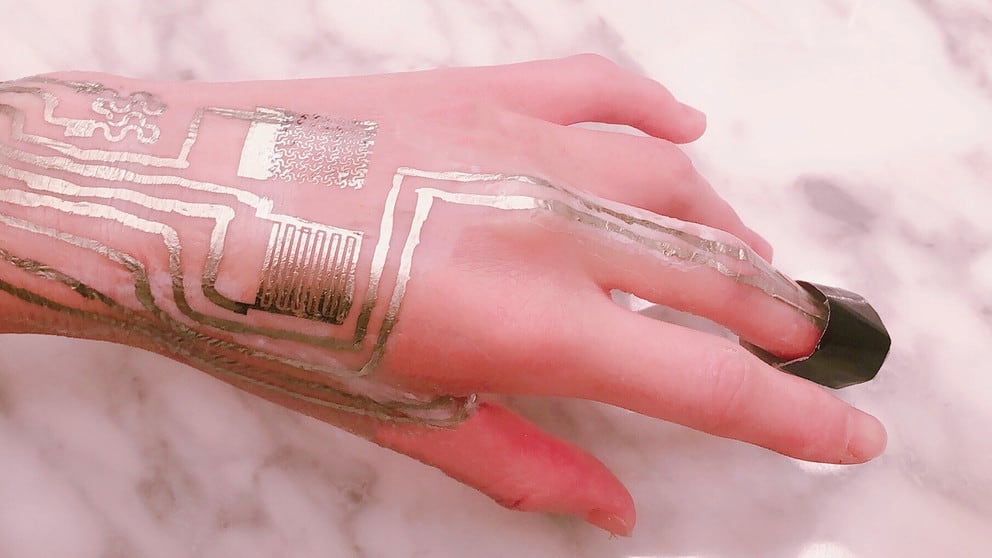
Breakthrough: Wearable sensors that can be printed directly onto skin
When the sensors are bonded to the skin, they can capture temperature, humidity, blood oxygen levels and heart performance.
Cheng and his colleagues are also working on wearable sensors that can be printed directly onto human skin without the use of heat.
Previously, the ability to print directly on skin had been hindered by the bonding process for the metallic components in the sensor. In a process called sintering, there is a requirement of temperatures of around 572 degrees Fahrenheit (300 degrees Celsius) to bond the sensor’s silver nanoparticles together.
“The skin surface cannot withstand such a high temperature, obviously,” Cheng said, so they proposed a sintering aid layer that would allow sintering at a lower temperature.
By adding a nanoparticle to the mix, they discovered that silver particles sinter at a lower temperature of about 212 F (100 C), but it was still too high for skin (even 104 F can blister skin). They changed the formula and printing material, and discovered that they could sinter at room temperature.
The sintering aid layer is made up of polyvinyl alcohol paste, a main ingredient in peelable face masks, and calcium carbonate, which is in eggshells. “The outcome is profound,” Cheng said. “We don’t need to rely on heat to sinter.”
When the sensors are bonded to the skin, they can capture temperature, humidity, blood oxygen levels and heart performance signals with accuracy and precision. The sensors can remain in place for a few days, then be easily removed in a hot shower, and ready to be used again without harming either the device or skin.
“That’s especially important for people with sensitive skin, like the elderly and babies,” Cheng says.